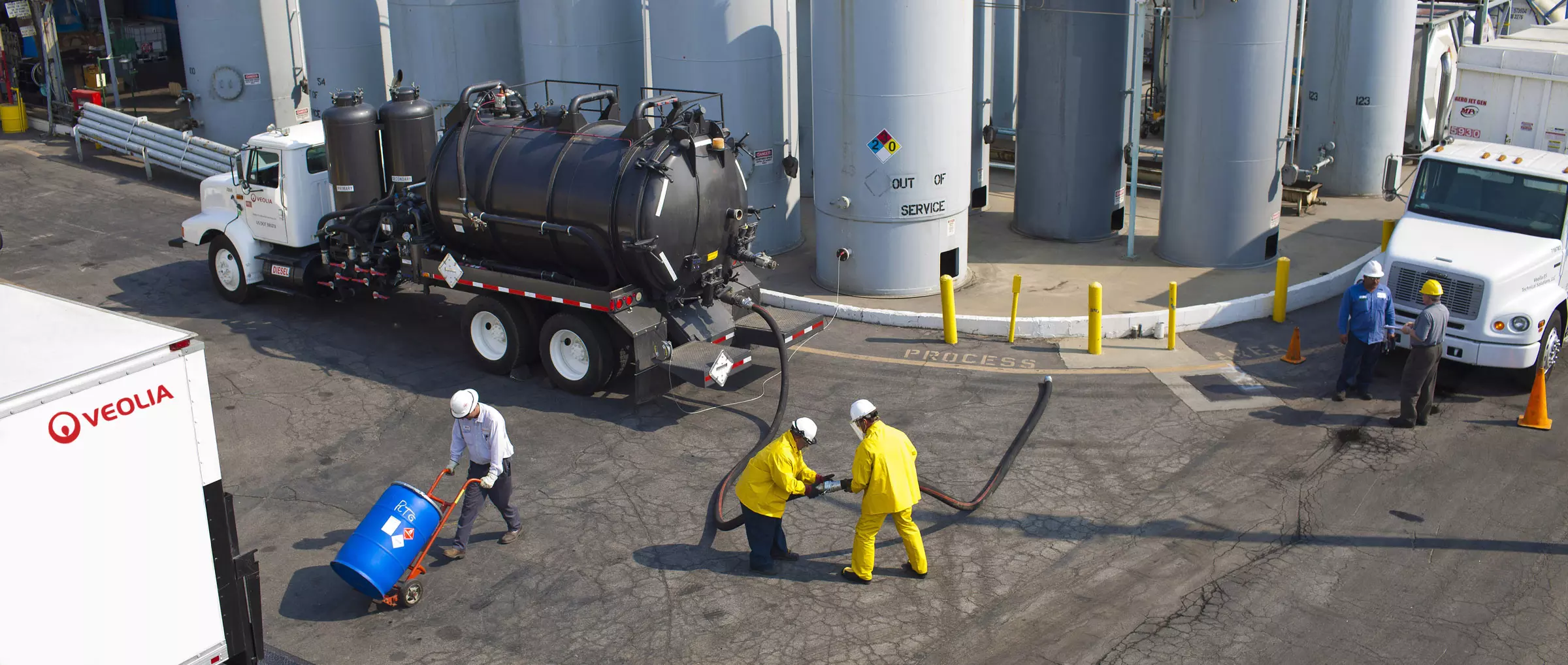
Previous Articles
Fuel Blending - An Interview with Dave Flood
Fuel Blending - An Interview with Dave Flood
“One of the post collection treatment options that Veolia provides is fuel blending, a service that recovers the Btu value of the customer’s waste stream. Our account managers discuss with the customer what their waste is, its characteristics, and from that we determine the best treatment technology for the waste codes associated with that material. Fuel blending is attractive to our customers from a cost and environmental perspective. It is more cost effective than incineration while recovering the heat value to make a product contributing to the circular economy.
“At Veolia’s site, we take in the waste and blend it to create a product that meets the end user’s specifications. We can receive waste in drums, totes, tankers and railcars and then bulk, blend and liquefy heavy sludges to prepare them for transport. Veolia’s niche is to supply the end user, a cement kiln, with millions of pounds of material per year from each of our fuel blending locations to help them reduce their reliance on fossil fuels.
“The fuel blending option is very attractive for many reasons. The waste fuel blend is used as an energy substitution at a cement kiln that is permitted to accept hazardous waste instead of burning coal, natural gas or oil. This hazardous waste is combusted to produce the intense heat needed to convert limestone and other materials into clinker, the primary ingredient used in cement. The heat produced is upwards of 3,000° F, and because of these extreme temperatures, there is very little ash that comes out of the kiln.
“Veolia is one of the largest suppliers of waste derived fuels to cement kilns in the country. We provide reliable, high quality fuel that meets our end users specifications every time.”
Dave Flood
General Manager, Gulf Coast Branch
Veolia North America, Industrial Business
EPA Hierarchy
Tracking the EPA hierarchy with Veolia’s Jim Dykhuis
“Everything starts with the hierarchy”
The EPA waste hierarchy sets forth a priority order of what constitutes the best overall environmental option for dealing with hazardous waste. Following the hierarchy can protect the environment, save money, prevent greenhouse gas emissions, reduce pollutants, save energy, and conserve resources. Jim Dykhuis of Veolia explains each level of the hierarchy to help you better understand possible solutions for disposing of hazardous waste.
Eliminate
“The EPA is trying to do everything possible to reduce and possibly eliminate waste, which includes product substitutions, when possible. For example, say you’re generating a paint sludge that’s hazardous because of a solvent. The hierarchy suggests that you explore potential changes to that paint, such as moving from solvent-based paint to electrodeposition-based paint. That way, you’ve eliminated what was making the paint hazardous, and any waste produced should no longer be an environmental concern.”
Reduce
“The next step in the hierarchy is waste reduction. Staying with the painting example, let’s say you’re unable to eliminate the solvent by using a substitute product. The hierarchy encourages everyone to explore alternative ways of reducing the amount of waste paint produced. For example, if you’re painting with a gun, you need to clean any attached hoses at the end of the day. By shortening the length of the hose, there is less solvent to dispose of, which is an example of reducing hazardous waste.”
Reusing
“Often waste is viable for use in another industry or for another purpose. An automotive company that needs to clean up their paint lines doesn’t need virgin solvent, and waste-derived solvent may be completely suitable for their needs. You can take your waste and provide it to them provided it qualifies as a legitimate reuse, and that is acceptable reuse under the EPA guidelines.”
Recycling
“Recycling is just what it sounds like: reusing solvents, rather than disposing of them. Veolia operates four facilities capable of recycling solvent that can clean up a waste solvent, so that it is suitable for use. The recycled solvent is then returned to the original user, which is called ‘tolling’, or it is put on the market and sold to a third party for use as any other virgin solvent.”
Treat
“The EPA has specified different types of treatment, based on what type of hazardous waste is being treated. For a lot of waste, treatment could include stabilization of a metal through the use of reagents. Once waste has been treated and stabilized, it could be landfilled with greatly reduced environmental concerns.”
Disposal
“Disposal is the last option the EPA wants people to consider under the hierarchy, and, ultimately, it means that the waste will end up being land-disposed or incinerated, and it’s up to the waste generator to work with a reputable waste services provider to explore options to minimize both their costs and environmental liability. Before waste is disposed of, the EPA wants companies to consider all the other possible solutions in order to reduce the total amount of waste that ends up being treated for disposal. That’s how the hierarchy works.”
Determining Proper Waste Management with Veolia's Jim Dykhuis
Waste Characteristics
"The chemical composition of waste is going to play a large Part in deciding where that waste ends up. Is the waste liquid or solid, acidic or basic, does it have high chlorine? For example, polychlorinated biphenyl (PCB) waste is probably the second hardes compound to destroy via incineration, behind dioxin. You can't just dispose of it anywhere, as it must be destroyed in a Toxic Substance Control Act (TSCA) permitted incinerator designed specifically for that task. If you have solids contaminated with PCBs, the chemical composition determines if it could be disposed of in a PCB permitted landfill or if they too would require incineration.
"There are practical considerations, too, like the physical state of the waste or what type of contaminants are in the waste. Wastewaters contaminated with metals could be incinerated, but are more economically managed at a treatment plant, where they can precipitate out the metals and discharge the water after proper filtration."
"When determining who can handle the waste and how it will be managed, the packaging of the waste should also be considered. Depending on whether it is stored in a fiber drum, tanks, tote, steel drum, poly drum or roll-off, handling and even the treatment, storage or disposal facilities (TSDF) may change. The ultimate TSDF may or may not have the ability to manage waste in certain types of containers."
Waste Classification
“Once waste is classified, a treatment standard can be determined. One consideration is whether there are any land disposal restrictions associated with the classified waste. For example, if an F006 waste byproduct containing chrome is generated, additional treatment would be required prior to disposal in a landfill. These considerations must be addressed to ensure efficient and compliant disposal methods are chosen.”
Generator Preference, Considering Liability
“The generator ultimately decides who disposes of their hazardous waste and how it will be treated. This can have far reaching implications on potential liability. The regulations create what’s known as cradle to grave liability, firmly placing responsibility for the waste forever on the generator. If a company is chosen solely for cost savings, the long-term results could be disastrous. These least expensive regulatory approved treatment vendors may cut corners, lack cash flow to support robust health, safety and environmental compliance departments or dispose of the waste improperly.
“A strong audit program is needed to vet potential environmental service providers and the ultimate TSDF used. In addition, hazardous waste generators need to evaluate the financial health and compliance history of their potential partners.”
Incineration - An Interview with Dave Flood
Incineration - An Interview with Dave Flood
“When a waste is marked for incineration, Veolia’s network picks it up and assigns an incineration technology based upon the material profile. Depending on the material, it is then consolidated and shipped to our incinerators for destruction or, in many cases, the material is shipped directly from the customer for destruction.
Waste will fit the profile for incineration destruction when it might not have high energy value or is toxic, reactive, or corrosive. Incinerators have sophisticated controls to protect against pollution and meet mandated air emission limits. An incinerator is permitted to take all these different materials, because we are required to conform to federal regulations and operate within their guidelines, some of which are described below.
The Port Arthur, TX incinerator accepts waste solvents, solvent/oil mixtures, organic and inorganic chemical wastes, pesticide wastes, petroleum wastes, aqueous wastes, contaminated soils, sludge, Polychlorinated biphenyls (PCBs), Texas Medical and capacitors, among others. Non-incineration wastes are also accepted and managed through our third party TSDF program."
Wastes that are prohibited are: radioactive or nuclear waste material, Class 1 explosives, and listed dioxin containing wastes, and municipal garbage. Waste codes that have specified technology treatment requirements may also be restricted unless the waste matrix is amenable to treatment by combustion.
Destroying RCRA and TSCA PCB Waste
"We feature a rotary kiln incinerator with a secondary combustion chamber (SCC) that is capable of destroying RCRA and TSCA PCB bulk solids, sludge, bulk liquids, and containerized waste. RCRA and TSCA solids, sludge, energetic liquids, lean water, and containerized wastes are fed to the kiln. Additionally, RCRA and TSCA energetic liquid wastes are fed to the SCC.
The kiln maintains temperatures above 1400 degrees F. In the vertical SCC, the current minimum operating temperatures are greater than 2000 degrees F.
The residence time of solids in the kiln is approximately 30 to 90 minutes and five to ten seconds for gases. Gas phase residence time in the SCC is two to five seconds. As the waste is heated in the kiln, organics will be destroyed in place or volatilized and subsequently destroyed in the SCC. The facility is engineered to achieve a Destruction Removal Efficiency (DRE) of 99.99999%.
Solid feed is introduced into the kiln via a container ram feeder, a bulk solids chute and a putzmeister (sludge) feed nozzle. Liquid feed is introduced through one of several waste nozzles. Small cylinders are handled through a cylinder box and fed into the kiln.
Liquid waste is introduced into the SCC via liquid nozzles and direct inject nozzles. Make up fuel for the burners and pilot is natural gas.
In the combustion gas purification train, the gases will be quenched from approximately 2000 degrees F to 185 degrees F using water and recirculated scrubber liquid, scrubbed for acid gases and larger particulates with an NaOH enriched scrubber liquid in two parallel packed bed absorbers and, scrubbed for fine particulates in two parallel train, four stage ionizing wet scrubbers (IWS). In addition, a Wet Electrostatic Precipitator (WESP) has been installed downstream of the IWS for compliance with MACT. The resulting cleaned flue gas exits the 130-foot stack and particulate emissions are significantly less than the 0.08 RCRA standard. HCl control efficiencies are greater than 99% thereby controlling HCL emissions well below the RCRA and CAA - MACT standards."
Dave Flood
General Manager, Gulf Coast Branch
Veolia North America, Industrial Business
Wastewater Treatment – An interview with Kevin McGrath and Mark Hemming
Wastewater Treatment – An interview with Kevin McGrath and Mark Hemming
Before wastewater is treated, classification is necessary for proper and safe disposal. “Veolia works with customers to determine what type of waste they have and how many gallons they generate,” says Kevin McGrath, Senior Manager of Environmental Affairs at Veolia. “Our team will then go in and specifically design a system that meets the customer’s needs. For example, we can coordinate off-site transportation and disposal, or we can build and maintain a system to treat the wastewater on-site.”
Once the general treatment requirements and the classification are established, the wastewater is transported for treatment, based on its characteristics. “Every classification ultimately revolves around whether the material is organic or inorganic,” explains Mark Hemming, Vice President of Key Accounts at Veolia. “Inorganic wastewater includes things like elemental metals or other contaminants, nothing that is biological. Organic wastewater involves any contaminants that has a carbon molecule. From industry this could be a water with a solvent layer or it could be something that is biological, like food.
Organic treatment
“Organic treatment generally involves using some type of microorganism to breakdown the wastewater. The process really just expedites nature’s breakdown process. If you set a sandwich on a plate and leave it on your back deck for a year, naturally occurring microorganisms will eventually break it down. We turbo charge those organisms by introducing oxygen, which speeds up their digestive process to break down the materials faster. In the end, you are left with a sludge that can be dewatered and safely disposed of in a landfill.”
Inorganic treatment
Inorganic treatment is more complicated, and first requires a determination on whether the materials are undissolved or dissolved. “Undissolved means you can look at a beaker of water, and you can see particles,” says Hemming. “Undissolved material can be observed and must be further classified into colloidal and settleable.
With settleable contaminants, you can use a tank where the water is calm and allows the particles to fall to the bottom, then you pull them from the bottom in various ways. You can separate the particles from the water and de-water them. If the waste is a less settleable, then we need a higher water quality and use filters to separate the materials. We can clean the filters or back wash and repeat the process until the water is clean. The remaining sludge can be dewatered and taken to a landfill for disposal.
“With undissolved material, the water is treated with a mix of chemistry and membranes. Collodial particles have charges that are so tiny that they don’t settle. They just float around in the water and need to be altered through chemistry and agitation or passed through a very fine filter to be removed. Water is pushed through a plastic membrane material that lets pure water through while storing the contaminated water. The contaminated water is concentrated at that point, and needs to be further treated to isolate the particles for disposal. This process is accomplished with different chemicals depending on the properties of the contaminants.
“When working with dissolved wastewater, we use chemistry to force the particles to solidify in the water. So if it’s a clear water stream, the dissolved material will reappear and the water will become cloudy. We then use the same process for undissolved water and filter the contaminants through a membrane.”
While the exact process differs slightly for various contaminant sources, ultimately the filtered water is reusable and the waste is extracted for proper disposal, providing sustainable solutions for wastewater treatment.
Solvent Recovery – An interview with Jim Reddy
Veolia has developed solvent recovery solutions that minimize costs for processing, transporting and disposal of waste. With proven, sustainable approaches, Veolia begins by evaluating the waste to determine the best approach to combine regulatory compliance with waste reuse.
“Solvent recovery is highly dependant on the characteristics of the waste stream that produces it,” says Jim Reddy, reclaim product line manager at West Carrollton, Ohio. “Veolia recovers waste steams from a variety of companies, from the pharmaceutical industry to chemical processing and beyond.
Once the waste stream has been classified, Veolia can determine what type of equipment is appropriate for recycling. “For example, if the waste stream includes solid materials, the solvent would first be processed with a wiped film evaporator, which basically removes any solids and color,” says Reddy. “Depending on if there was additional recycling needed, the solvent could then be placed into one of the distillation columns for fractionation.
“This is where solvent recovery can become complicated, because it requires more than one step. In addition to distillation columns, we also have a piece of equipment called the molecular sieve, which will remove water from the solvent. Sometimes during that process the solvent can pick up color again, which means it would be put back into the wiped film evaporator.”
Wiped film evaporator
The wiped film evaporator is a heated cylinder, similar to a distillation column, but includes a rotor going down the center of the column. Attached to the rotor are paddles, which operate much like a blender. “When you introduce a liquid or solvent to the system, the solvent is spun up against the heated walls where the solvent is vaporized and the solids are left behind for disposal.”
Distillation column
A distillation column is a tall, heated cylinder that houses a number of trays inside at various heights. When you heat up the column there is a temperature difference between the top and bottom of the column. Where the heat is introduced at the bottom, the trays will be hotter, and the trays at the top of the column will be cooler.
“Every chemical has a different boiling point, so the chemicals will reflux, vaporize, and then condense multiple times as they move up the trays,” explains Reddy. “This allows the different solvents to separate from the base at their boiling point. The higher boilers will stay at the bottom of the column, while the lower boilers, and contaminants, will concentrate at the top.”
Molecular Sieve
A molecular sieve is a material with microscopic holes, or pores, which allow the passage of small molecules through absorption. Larger molecules cannot be absorbed through the pores, so it’s ideal for separating different elements.
“At our facility, we can run solvent through the sieve and successfully separate it from any water in its composition. This allows us to purify the solvent completely, so we can then recycle or repurpose it.”
Tolling versus fuels
Veolia works with many different industries to recover waste streams. “Chemical processing and pharmaceuticals are probably the two biggest, but we also work with companies that use paint, such as automobile or cabinet manufacturers.”
At all four of Veolia’s facilities, both solvent recycling and fuel blending are offered. “Tolling, returns a company's solvent to reuse in their process without the need for disposal, while fuel blending takes used solvents that are not recyclable and repurposes them into fuel for certain industries, such as making cement.
“We do a lot of tolling for companies that will have a solvent they’re using from a specific manufacturing process that can be recycled and reused,” notes Reddy. “We work with these companies to obtain the product specifications they need, and then return it to the customer for reuse in their process.”
With fuel blending, any solvent that isn’t suitable for reclaim would go straight into fuels. "The fuel created from used solvents is ideal for making Portland cement, which is a product manufactured from limestone using large amounts of energy. The cement kiln will replace some or all of their coal fuel with solvent fuels.”
Tailored solutions
While Veolia’s facilities handle large quantities of solvents, there are also solutions available for smaller waste streams. “Veolia will work with customers who have smaller quantities and look into installing on-site recovery units to handle the same process in our facilities,” observess Reddy. “If a customer has a very large waste stream, we often investigate whether they can save money on transportation costs by designing and installing a system on their property.”